The Sequence Solution: Accelerating Knowledge to Increase Speed to Market through Commissioning, Qualification and Validation (CQV) Services
With more than 20 years of experience in Commissioning, Qualification and Validation (CQV) and Digital Solutions consulting for our clients, Sequence has an in-depth understanding of the many challenges and common struggles involved in bringing a facility online to meet FDA regulations.
Sequence has executed a vision to build a fully functional pharmaceutical manufacturing training facility to educate and prepare our team of consultants in a way the industry hasn’t seen before.
We’re providing exposure to process equipment and software applications in a real-life setting. We intentionally include a wide range of systems and software our consultants will encounter on job sites to increase their knowledge across multiple platforms.
This level of exposure and hands-on experience, together with education on the latest industry trends, provides the advantage of accelerated knowledge equivalent to years of experience in many cases. This allows our consultants to be immediately impactful on the job site no matter how many years they’ve been in the industry.
How our approach to the CQV training process sets us apart
Our cross-functional approach to training our consultants is unique and provides greater value for our clients and employees because we’re teaching risk mitigation through the understanding of implications and impact to all areas within a facility. This is further enhanced by our hiring practice based on our ideal candidate profile to ensure success from the beginning.
Our revolutionary training facility allows us to provide continuing education for our more experienced team members and accelerated learning for newer team members. This includes:
Direct exposure and hands-on learning with equipment and systems in a real-life application setting.
Targeted training focused on translating product and process knowledge into quality driven design requirements and efficient risk-based testing strategies.
Exposure to a wide range of Digital Solutions including BMS, PCS and MES.
Accelerated training that provides the equivalent of years of growth and development in a short period of time.
Incorporates all elements to conceptually train resources on all aspects of plant operations: facilities, utilities, lab, IT, manufacturing process (upstream & downstream), filling, automation, and ancillary equipment with a Pharma 4.0 infrastructure.
A Cross-Functional Approach to Commissioning, Qualification, Validation (CQV) & Digital Solutions
Our hands-on training facility is set up to represent a mock pharmaceutical manufacturing facility with five core areas of focus for our training: Facilities, Equipment, Utilities, Lab and Computerized Systems.
Traditionally, these areas within a pharmaceutical manufacturing facility are managed by siloed departments and there are deficiencies in collaboration and knowledge transfer between them. We have determined that a cross functional understanding of how all these supporting systems, across all core areas, impact one another is paramount to correctly establishing that intended use has been achieved.
The program is focused on making sure our employees develop an understanding of how to apply both regulation and guidance to the validation lifecycle, specifically focusing on design, commissioning, and qualification of new facilities.
In addition, we provide exposure to the latest Industry guidance, so they understand what it takes to create strategies to achieve compliance. This includes ISPE, USP, ICH, FDA and ISA.
The rapid acceleration of knowledge is what sets our team of consultants apart by creating a level of understanding that will ultimately increase speed to market for the life impacting drugs our clients are manufacturing.
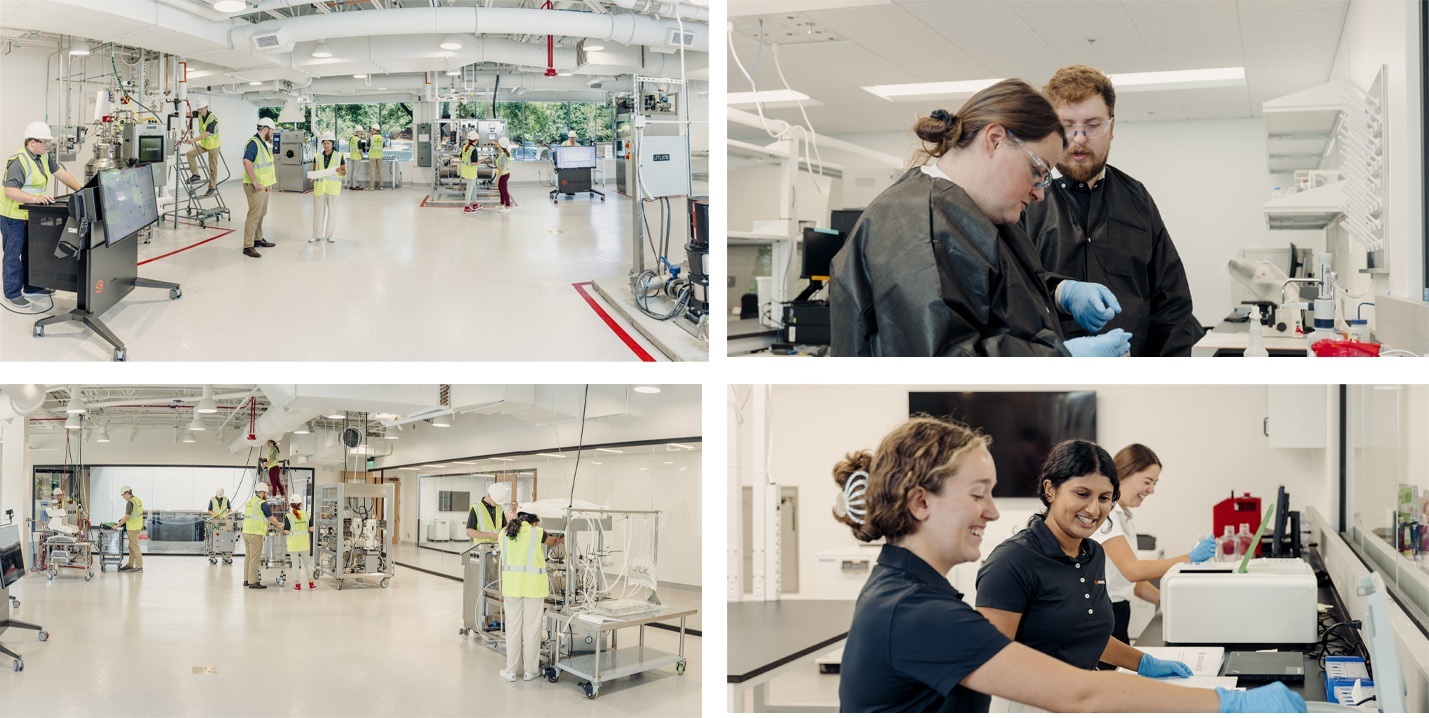
CHALLENGE: Lack of technical and process knowledge
Resulting Issues on the Job:
- Risk assessments that are performed inaccurately result in missed design flaws, creating timeline impact
- A lack of process knowledge translates to a more conservative mindset, resulting in excessive, unnecessary testing
- Lack of process knowledge can even result in “design as you go” mentality
Sequence Quality Solution:
Our comprehensive training includes taking our team through risk assessments to teach them the critical quality attributes of a product that translate into critical process requirements. In addition, we provide access to risk assessment tools and strategies from a wide variety of projects, processes and equipment they’ll encounter on a job site. Supporting all of this is a repository of knowledge from our entire consultant base spanning 20+ years of experience in CQV and Digital Solutions.
CHALLENGE: Inability to proactively identify potential risks
Resulting Issues on the Job:
- Without cross-functional insight, there is limited ability to identify and visualize issues that will have a tangible, adverse impact to the project
- With limited process knowledge, project timelines will be at risk while teams wait for other departments to deliver
Sequence Quality Solution:
In order to truly be efficient and effective, testing should not be approached as a “checkbox” exercise. We know that understanding the big picture of the entire process is key in identifying potential risks. Our training is designed to equip our resources with a level of knowledge to understand project requirements that will enable them to question a specification and suggest better options if it will improve the overall process and reduce risk.
CHALLENGE: Overcoming cross-functional boundaries
Resulting Issues on the Job:
- When developing a URS, FS etc., the inability to have open lines of communication across multi-disciplined departments will negatively impact project timeline
- A siloed departmental approach to communication and completing deliverables hinders project success
Sequence Quality Solution:
By training our team members on the primary areas of manufacturing, we’re teaching them to understand how potential issues in just one area could impact the entire process. They’re learning from the perspective of all departments so that when they're working on site, they understand the critical need to proactively communicate with the various teams, such as quality, at the right time to keep the project moving forward successfully.
CHALLENGE: Project team that requires too much oversight
Resulting Issues on the Job:
- A team with limited understanding will typically view the commissioning and qualification process as a checkbox exercise rather than taking a proactive approach to efficient project execution
- Ineffective teams will tend to sit back and wait to be told what to do
Sequence Quality Solution:
We’re taking steps to ensure our engineering consultants understand project objectives so they can be effective in overcoming barriers to keep projects moving with limited client input. With this insight, they can work proactively toward the ultimate project goal and play a vital role in keeping the project on track to mitigate potential risk that will help get our client’s products to market faster.
What is the C&Q process?
Commissioning and Qualification (CQV) are integral processes in the pharmaceutical manufacturing industry, essential for ensuring the quality, safety, and efficacy of pharmaceutical products. The primary objective of CQV is to systematically validate that the equipment, systems, and facilities meet predefined standards and are capable of consistently producing pharmaceuticals that adhere to stringent quality requirements. These processes are mandated by regulatory authorities to uphold the highest standards in pharmaceutical manufacturing.
Commissioning (C), the first phase of CQV, involves a meticulous approach to verifying that all aspects of a facility or equipment align with the operational requirements outlined by the owner or final user. This includes a thorough design review to ensure adherence to specifications. Installation Qualification (IQ) confirms the correct installation of equipment, while Operational Qualification (OQ) ensures that the equipment functions within specified parameters. Functional Qualification (FQ) goes further to validate the equipment's performance in simulated or actual production environments. Throughout these activities, comprehensive documentation is crucial to record all processes and results.
The Qualification (Q) phase builds on the foundation laid during commissioning. It encompasses activities such as Performance Qualification (PQ), which demonstrates that the system consistently produces the desired results in a production environment. Process Validation, a subset of Q, establishes documented evidence that a process consistently produces a product meeting predetermined specifications and quality attributes. The Validation Master Plan (VMP) outlines the overall strategy for validation, providing a roadmap for the entire CQV process. Change control procedures are established to manage and document any changes made to qualified systems.
Documentation and record-keeping are pervasive themes throughout CQV, ensuring that every step of the process is thoroughly documented. This documentation is not only a record of compliance but also serves as a critical resource for future reference and continuous improvement. Regulatory compliance is paramount, with adherence to guidelines from health authorities such as the U.S. Food and Drug Administration (FDA) and the European Medicines Agency (EMA). Personnel involved in CQV activities must undergo rigorous training to execute the processes effectively, contributing to the successful validation and maintenance of pharmaceutical manufacturing processes and equipment.
In conclusion, the Commissioning and Qualification process, an essential aspect of Good Manufacturing Practice (GMP), provides a systematic and comprehensive framework for achieving and maintaining the validated state of manufacturing processes, ultimately ensuring the production of high-quality pharmaceuticals.
What is the difference between validation and qualification?
Validation and qualification, while closely related, serve distinct roles in the regulated industries, particularly in pharmaceutical manufacturing. Each plays a crucial part in ensuring the quality, safety, and efficacy of products, adhering to stringent regulatory standards.
Qualification is a more focused process, honing in on equipment and systems. It involves obtaining and documenting evidence that these components are correctly installed, operate within specified parameters, and consistently deliver expected results. The qualification process typically encompasses three key stages: Installation Qualification (IQ), which verifies proper installation according to design specifications; Operational Qualification (OQ), ensuring that the equipment functions as intended within predefined parameters; and sometimes, Performance Qualification (PQ), demonstrating consistent production of results meeting predetermined specifications in its intended environment. Qualification is essentially a prerequisite for the broader validation process.
Validation, on the other hand, is a more encompassing procedure that extends beyond the confines of individual components. It involves providing documented evidence that a system or process consistently meets predetermined specifications and quality attributes throughout its lifecycle. Within the realm of validation, Process Validation focuses on ensuring that a specific manufacturing process consistently produces products meeting predetermined specifications. System Validation ensures that all components within a system or facility work cohesively to consistently deliver desired results. Additionally, Cleaning Validation ensures that the cleaning processes employed are effective in preventing cross-contamination. Validation, therefore, represents a holistic approach, considering the entire system or process rather than just individual components.
In summary, while qualification serves as a vital step in ensuring the reliability of equipment and systems, validation takes a broader perspective, encompassing the entire process or system. Both are indispensable in meeting regulatory requirements and upholding the standards of quality in industries governed by strict regulations, such as pharmaceutical manufacturing. Together, they form a comprehensive quality management system essential for the integrity of the manufacturing processes.