The latest Veeva Training Solutions podcast episode reveals what regulators really want to see in GMP manufacturing: a deep understanding of your processes.
Justin Cook, Chief Technical Officer at Sequence joined the Veeva Training Solutions podcast to discuss how Sequence's innovative hands-on training facility is revolutionizing employee development and driving business success. Justin also talks about the 5 Pillars of Manufacturing and how they are integrated into their training programs to ensure quality, safety, and efficiency.
You can read the full transcript below or LISTEN TO THE PODCAST HERE.
***
Moderator: Graham O’Keeffe is the General Manager at Veeva LearnGxP.
Guest: Justin Cook is the Chief Technical Officer at Sequence Inc.
GRAHAM: Hey everyone, and welcome back to the Veeva Training Solutions Podcast. I'm delighted to be here today with Justin Cook. Justin is the CTO of Sequence. Justin, welcome to the podcast, and if you want to do just a brief introduction, feel free.
JUSTIN: Thanks, Graham. My name is Justin Cook, I’m the Chief Technical Officer here at Sequence. What that really means is I oversee the acquisition of talent, and the training of that talent so we can mobilize consultants across the US to support our life science clients in trying to purchase, design, procure, install, commission, qualify equipment that ultimately helps them get to a compliant state of control where they can deliver drugs to patients faster. So that's a little bit of background. I can go into a little bit of how I got here. I entered the industry in 2007. I've got a mechanical engineering background and came into the industry doing process automation. So I was behind a computer screen quite a lot. And moving into probably 2011 I got some more opportunity to be out in the field working with equipment. It was very eye opening to have a chance to put my hands on equipment, which drives a lot of the passion behind why I prefer our team to get hands on exposure. In 2013 I started to lead projects, and that’s when project management really became a skill to put on my tool belt. Moving into 2016, 2017 was managing various scopes, which leads into the cross functional passion that I have, 2018 stepped out of the field and started a training program here at Sequence.
GRAHAM: Good stuff. Thanks Justin. And this is a really exciting podcast. It's a little bit different because we're coming at it from the standpoint of hands-on training, shaping a modern GMP and manufacturing environment. I think this is really different for us, because we're talking about getting people ready to go into organizations you work with, to get them ready from day one so they can be proactive in terms of hitting the ground running. And that's no that's no easy feat to do, right?
There's lots of things involved in getting somebody knowledgeable about compliance and ready to work in a GMP manufacturing environment. So my first question on that is, you've created a really modern, hands on training facility, and that's probably something you've thought long and hard about, and the cost involved to do that. How did you conceive that idea? Or why did you think that was a good idea?
JUSTIN: As I mentioned, coming out in 2018 there was a lot of groundwork to be laid with regard to what the skill sets are that we feel are valuable, that our clients need us to possess.
And then, of course, you quickly shift to, how are we going to equip these people? What is the best approach to try to accelerate learning?
Once I kind of laid the groundwork of the program, I basically cast a vision of what types of concepts, what types of areas do we need to expose our folks to it? That quickly transitioned to, how do we invest into some type of hands-on equipment? Because we quickly realized white board training was just too much material, too fast, without an opportunity to apply the theory that was being shared. There's certainly a point of necessity for sharing the theory because you have to build a foundation. Because if you just have hands on, you go out there and just tell someone to stroke a valve, and hope that that's going to stick, they kind of need to understand what the purpose of the valve and why it’s there.
So it transitioned into a portion of the training being theory, a portion of it requiring this hands on. And so we invested into a small, what we call our solution prep vessel, a 150 liter vessel that we had. And we, we poured some money into it to automate some valves and some other devices that allowed us a chance to actually put water in it and talk to folks about sequence of operations and what clients are really needing us to know to be able to appropriately commission and qualify this stuff. So once we had that in place, it set the vision that we actually would love to expand from that one vessel to a multitude of unit operations that actually give us the opportunity to expose all the concepts that, whether it's at a different scale or different manufacturing science, that folks can walk into that environment and feel comfortable and confident to go apply the skills that they've acquired.
GRAHAM: What kind of ROI have you observed from doing this? Are your guys ready to go day one, going into a new facility, or what's been the kind of output of that?
JUSTIN: We certainly don't say that it's been an easy road. I mean, when you talk about our objective here it’s first of all to create a best in class resource that gets exposure at an accelerated rate.
And that's just uncommon in our industry, right? My own experience was more of an organic growth where it was based on what project you might have gotten a chance to be a part of, and what equipment or systems or manufacturing science was being conducted on said project. And so you find in the consulting industry that it’s very dynamic, and can be a much different experience for different resources. We wanted to streamline that. We wanted to be in control of that experience.
So we took the raw material, if you will, which would be our incoming talent. We put a lot of energy into what type of talent we needed to start with in order to accelerate their growth. We spent a lot of time identifying the type of resource, and then we injected this training into that raw material, if you will. And basically, we're generating something that I would argue the industry has not been used to, which is someone that has exposure in an intentional and purposeful way, rather than waiting for that resource to have 15 years on a resume. That never truly reflects actual exposure so we wanted to overcome that problem.
GRAHAM: Yeah, I think that's really novel, actually, and I kind of see it as it's nearly on the job training before you go on the job.
JUSTIN: The challenge is trying to convince our clients that you can take 15 years, that everyone has on their resume and that’s how they got their talent and skill set. And so now you're going to consolidate that and go, No, we're going to present you with a two year person that we're going to argue has that same skill set in a condensed amount of time. So the ROI is coming. Our brand is shaping up at an accelerated rate. We're seeing the buy in that's happening, but it's been quite the challenge, been quite the road that we've been walking to convince our clients that this is something that is feasible and something that can actually be brought to reality.
GRAHAM: Yeah, I can imagine. Kudos to Sequence. It's definitely a novel approach, and I think the industry needs it actually as well. So let's kind of change direction a little bit, to talking about a GMP environment. We're talking about modern training, but in a GMP environment, talk to me a little bit about the main pillars of manufacturing. Justin, what's your viewpoint on that?
JUSTIN: Yeah, absolutely. And that's really where I was talking about, kind of setting the vision to start with. It's almost like you're trying to start with an empty canvas, trying to determine what it is that it is the pinnacle of learning? What is it that we should suggest is the maximum amount of learning that we want to expose our folks to? And it took us into this mode of saying, You know what? If you go into any pharmaceutical facility, they're going to need to be controlling HVAC right there. The HVAC is a very critical part of controlling particulates and to satisfying some of the FDA requirements in part 211, as well as annex one, and things that we're seeing come on the scene.
So we consider that for a facilities pillar, you need to understand that the types of material you use, the surface finishes, the cleanability, of all those things, combined with HVAC and warehouse control and CT use and things of that nature. And then you've got the manufacturing equipment, which can vary between solid dose, or you've got fill finish operations. You've got this cell and gene therapy. So manufacturing sciences drive different unit operations, but there's consistent concepts from within. Then you've got utilities that are prevalent. Basically anywhere you go, you've got your air and water and clean steam and plant steam, things of that nature. And then you've got laboratory stuff, so analytical, microbial analysis, is very prevalent as well. And then you've got computerized systems, right? A lot of these things.
Now, in a digital transformation world that we live in, there's a lot of networking principles and concepts that are necessary to understand, because traditionally, maybe you could walk out with a lot of manual tasks. Now it's a lot of integrated pieces of equipment that are tying into this huge data lake of information. So those are the five that we really put a lot of focus on, because we believe those are relevant regardless of what's being produced. You could almost make the argument that even across industries, you could step into automotive and facilities that are requiring some of those same things.
GRAHAM: Even as we've gone through those pillars, there is so much to understand, right? And somebody who's maybe new to the industry to get them trained on all those different types of aspects. It's really beneficial, right? Because I know a Legacy way of learning within organizations is that you go in, you don't get that holistic view of what it's like to work in these environments. So I think that's something we should all think about deeply in terms of all of those different pillars, you also touched on the FDA, right? We all know why that's important, and the alignment with the FDA in terms of manufacturing. How do your training programs align with the FDA guidelines? And you've mentioned things like 211, annex one, just kind of maybe talk me through that a little bit.
JUSTIN: We'd like to consider ourselves compliance minded engineers. And the goal there is to plug a lot into arguably the good engineering practice world, where some of these projects are when they start to grade, then the path and the placement of the facility, they start to erect the steel. There's a lot of good engineering practice that needs to go into formulating a facility that's ultimately operational. But then there's the regulatory bodies that suggest, you know what, this also has to be a compliant, repeatable production process that is protecting the purity of the product. It's protecting and ensuring the efficacy that was defined early on in some of the drug development processes. The understanding of the regulations is paramount and serves as a foundation that we build upon, because everyone needs to maintain the end goal as they're starting to support the design and other things.
But I would argue what I when I first came into the industry, there was a huge emphasis on “let me just prepare a lot of documentation,” and hopes that that's going to be attractive to this regulatory body that's going to come in here, and expect that I'm going to showcase all this mountain of documents and hope that that would get their buy in, that I have repeatable production process. We are now in an age where the FDA is trying, in my opinion, to reinforce that that's not what they're looking for. What they're looking for are clients where the manufacturers themselves understand the product that they're producing, there needs to be critical thinking. And so where I would say our training program aligns is that we're trying to generate critical thinkers by showing them, at a component level, how a valve interacts with the product. How do the pipes interact with the product? Can there be compatibility issues. Are there flow rate concerns? How do we maintain the critical process parameters so that we can ensure that the quality attributes that were defined ahead of time are going to be hit and maintained consistently and repeatably for that manufacturing process?
We're trying to break it all the way down at the component level to generate critical thinkers that I think the FDA and other regulatory bodies across the world are saying, Hey, we don't want your mountain of documentation. We want the documentation that proves that you have a very well thought out understanding of how your process is achieving a repeatable product that's going to be safe and effective for the consumer.
GRAHAM: I think that you summed up that really well. And I think a lot of companies are waking up to the fact that SOPs alone, it's not going to cut it anymore, right? And we see that a lot, even in terms of inspectors going into facilities, they're looking to see beyond SOP training, how are you really training people to be sufficient in the knowledge of what's happening on the manufacturing floor, and just to be aware of things that are happening around you, things like, why is cleaning validation important? Why do you have to have a qualification of a piece of equipment? You know, these are people processes we do on a daily basis. You know that overall, overarching understanding, I think that's where your training program is really beneficial.
Then for people going into the field, let's switch gears a little bit as well. Justin, in terms of variety of training, how have you effectively integrated hands on training with other types of training, like online training, or whatever it might be, whatever kind of modality you use, but that blend of training, I guess? How does that work?
JUSTIN: So obviously you run into challenges with timing. I mean, you can't just indefinitely train someone non stop without actually letting them go and utilize the skills that they've learned to go add value in this whole world that we find ourselves in of making drugs that patients need. So you can't just indefinitely, throw them in a closet and just have them train. And so we've got to find ways to accelerate that make that efficient. I think what we found is a good mix. If I can throw the school system under the bus for a moment, I think where they struggled was a teaching a lot of theory and struggling a little bit with the application.
So you've got folks that get exposed to the textbooks, they get exposed to the calculations. They're trying to formulate a foundational understanding, but they're limited in how they apply that, so therefore retention is impacted, etc. What we've tried to do is increase the hands on application, but you can't forego the theory. That was the point I was making earlier, that you've got to still build a foundational understanding so that the people know what they're putting their hands on, that they can go out into the field and recognize this is the purpose of an SOP. So we had to introduce things, and this is where we've also benefited from some of the stuff that Veeva has in the Learn GXP platform brand that you know our relationship stems back to because we've utilized some of that content to build a foundational understanding that helps us accelerate our time, to get them out in front of this hands on equipment, because we don't need to spend as much time building the foundational understanding of what GDP is, or what part 211 is, or what the concept of validation is, because those are things you'd argue we have to spend a lot of time with someone who's starting from zero. You need to build that foundational understanding before you're ready to take them out and go, Okay, now I want you to implement and apply everything that I just taught you. So that's the blend of training I feel like is important, trying to minimize how much theory without partnering with the application. And I think it is a mix, right? There's no silver bullet to this. There's not one SOP you're going to read that’s going to make you qualified, you're going to do some hands on training. You're going to do some online training. It is a blend of everything, right? And it's done on a regular cadence so you have that knowledge going forward.
GRAHAM: So yeah, that's really important. Justin, I'm glad you pointed that out. Talk to me a little bit about Sequence and your future plans in terms of how you're doing this facility in general, what you're looking for in the next two to three years?
JUSTIN: Thanks for asking that question, Graham. You know, arguably our, if I can call it bread and butter, you know, where I think we've impacted the industry over the last 20 plus years is in this world of qualification and validation. But there's more to it than that. I mean, as we're talking there's things that the FDA is endorsing, such as risk-based efforts, some of that leans heavily into, again, back to those good engineering practices of startup commissioning efforts that are vital into ensuring that there's going to be a successful and repeatable production process that's full of qualified equipment in order to start that up and commission it.
I believe the industry is starving for talent that can go in there and understand how to start up a pump, how to ensure that the supply fans and HVAC systems are working appropriately. That takes more than an SOP training or a do it online course. So what I think we're hoping to strive for here is to expand ourselves left in the life cycle, if that makes sense, meaning that we really see that the skills that our people are possessing and that we're equipping them with can close a gap in talent that I believe is needed in order to review submittals for product purchases, whether that's OEM skids like a WFI still or it's the stick built components like valves and instrumentation that goes into distribution systems, sometimes you run into times where the process engineers that are on site, other folks supporting that, they run out of time to be able to appropriately review submittals, and then that causes downstream impact, that delays the project, etc. We want to see our folks engage earlier on in this process, partnering with construction managers and others to see that. That's a value add early on, but you got to have the right talent, and the folks that have the critical thinking mindset of knowing what we're trying to achieve in the end, that way, they're always putting their mind downstream while working on something two years in advance, right?
So, reviewing drawings, reviewing design, supporting that effort in an appropriate way, backed with having the right skill set that can hopefully alleviate downstream problems, where we constantly see, you know, the wrong valves installed the wrong instrument installed, the wrong tuning, the wrong automation, you know, list goes on that could hopefully be rectified very early to streamline all of these processes.
GRAHAM: We've covered a lot there, Justin, just a recap, we've gone through Sequence’s approach to shaping modern GMP manufacturing. I mean, you spoke a little bit about hands on training within the facility itself. We spoke a little bit about the five pillars of manufacturing as well, like, utilities, equipment, etc, etc.
We touched also on the FDA, which I think was really important when you mentioned that in terms of annex 1 and 211, all these things we should know as well, a blended approach to training and then your future plans. Any takeaway for anybody listening to this in a manufacturing training environment, any kind of best practices you want to share, or just maybe one takeaway that you've learned over the last 20 years?
JUSTIN: If I could summarize, we've got a lot of technological shifts that I think, whether it's manufacturing operators, if it's supervisors, if it's consultants, supporting any element of the project, life cycle, critical thinking skills and a strong understanding, a strong basis of what we're actually doing, and getting a little bit away from. I don't want this to come out wrong, but a paper jockey or a clipboard jockey, you know, and I say that because I was one. That's right, that's how I entered the industry. So, you know, hoping to get a little bit of meat on the bone behind what is being documented on the paper, and why are we documenting it? I think is important for all parties involved to help accelerate and streamline getting drugs across the line faster. For our patients, we're no longer in a world where we can delay and delay and delay because we're trying to figure it out. I think we've got to get in front of it, and in order to do that, we've got to increase talent. We've got to increase cross functional understanding. We have to bring digital solutions into the picture so people with a mind that can embrace complex topics like process automation, manufacturing execution, systems, full digital integration, those things are coming to us, and they're coming to us fast. And I think that's a big takeaway, we have to pour more into talent and skill set acquisition. And you know what's amazing we got through the whole podcast, and we didn't even mention AI. So that's a whole other one, right?
GRAHAM: That's a whole ‘nother ball game too, that's coming at us shifting quickly, and things change fast. Listen, Justin, thanks very much. It's been really insightful to speak to you and get that perspective from the consultancy aspect of the business. We'll definitely have you on again in the future to see how everything's going and the progress you're making over the next couple of years.
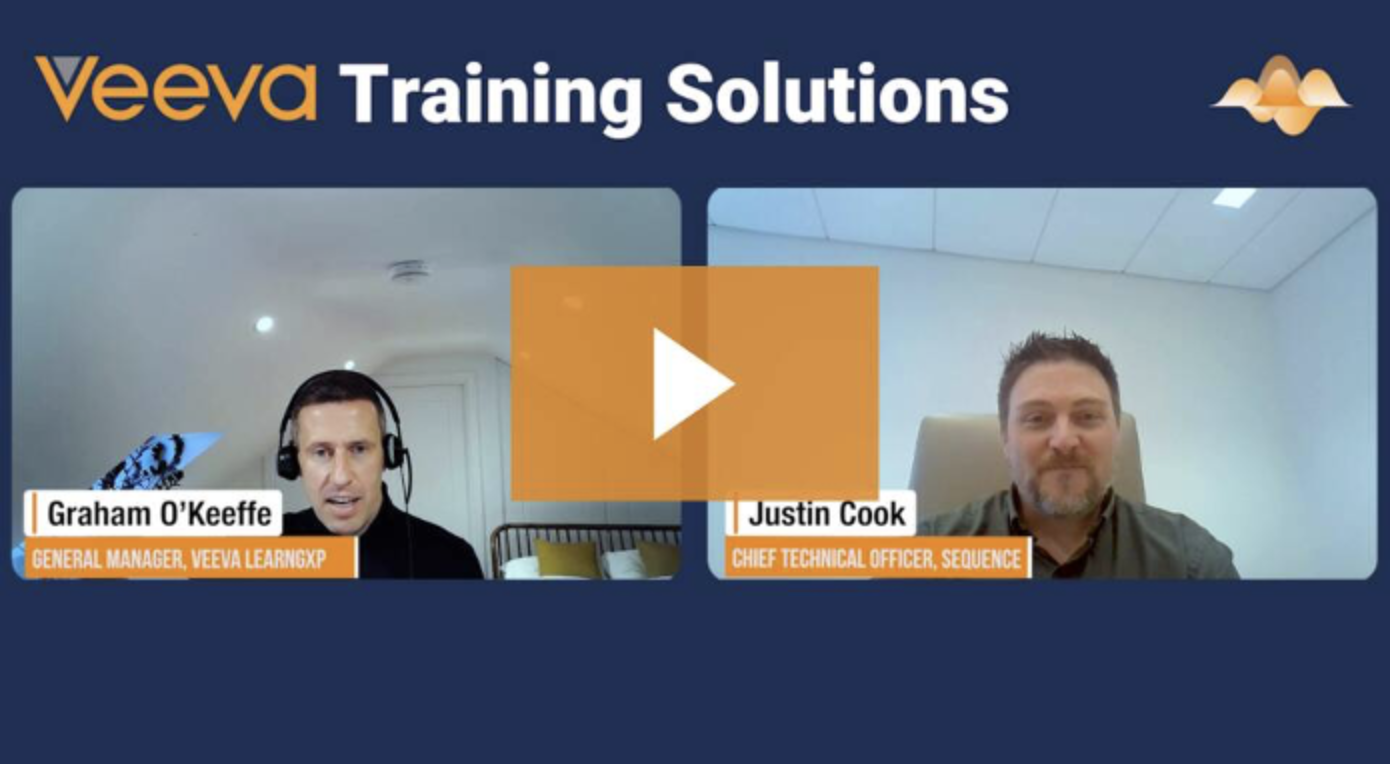
The podcast discusses how Sequence's innovative hands-on training facility is revolutionizing employee development and driving business success as well as the 5 Pillars of Manufacturing and how they are integrated into their training programs to ensure quality, safety, and efficiency.