Sequence is now offering hands-on pharmaceutical manufacturing operations training for external organizations.
The Sequence fully functional mock pharmaceutical facility allows us to train teams in five key areas: Facilities, Utilities, Equipment, Computerized Systems and QC Lab.
Sequence offers both standard curriculum courses and customized course options to fit a variety of needs. Just a few of the courses currently offered include upstream and downstream processing, aseptic techniques, PCS/MES and more.
A key benefit of customized training at Sequence is our ability to incorporate your internal organization’s SOPs and other procedures to develop a personalized program for your team. The best part is that your team will learn in an environment that is free of distractions, without the risk to your manufacturing line or product quality.
OUR QUALIFICATIONS
Sequence has spent the last 23+ years offering consulting services in Commissioning, Qualification and Validation (CQV) and Digital Solutions for some of the top pharmaceutical manufacturers in the world. This in-depth understanding of equipment and processes equips our team with the ability to teach the “why” behind concepts relevant to manufacturing as well as develop customized curriculums that are easy to understand and immediately impactful in terms of product quality, patient safety and driving results to the bottom line. Our training facility offers us the ability to provide manufacturing operations training that is a natural extension of these core services.
THE IMPACT OF A HANDS-ON LEARNING APPROACH
The benefits of incorporating a hands-on approach to education are proven. Hands-on learning is significantly more effective than traditional methods, with studies showing students retain significantly more information and develop deeper understanding when actively engaged in learning activities that are interactive, engaging, and relevant.
The benefits of hands-on learning include:
Improved Skill Retention and Practical Understanding
Engaging in real-world scenarios helps operators retain information better compared to a singular focus on theoretical training.
Increased Compliance with Regulatory Standards
Training in a controlled environment reduces the risk of compliance violations and reinforces conformity across the team when it comes to following SOPs and adhering to industry guidance.
Reduction in Human Errors
Familiarity with equipment and processes builds confidence and minimizes mistakes that could lead to product recalls or contamination. We intentionally create impactful moments of “sabotage” within our curriculum to provide challenging scenarios that may be encountered in real life.
Enhanced Problem-Solving and Critical Thinking
We create hands-on scenarios that allow operators to troubleshoot issues in a controlled setting without fear of making a costly mistake. Through this process, they learn to respond to real-life deviations and process failures that will improve decision-making during critical moments.
Better Equipment Handling and Maintenance
By providing practical experience it improves understanding of calibration, cleaning, and validation procedures which can result in reduced downtime.
Increased Safety Awareness
Real-world practice ensures operators are well-versed in workplace safety, cleanroom protocols, and proper use of Personal Protective Equipment (PPE) which reduces the likelihood of workplace accidents and contamination risks.
Faster Onboarding and Productivity
Hands-on training helps new employees learn faster and become operational more quickly by accelerating skill development compared to purely theoretical approaches.
Find out more about the ways Sequence can support the training needs for your organization.
Contact us at Training@SequenceQCS.com or Download our Training Brochure
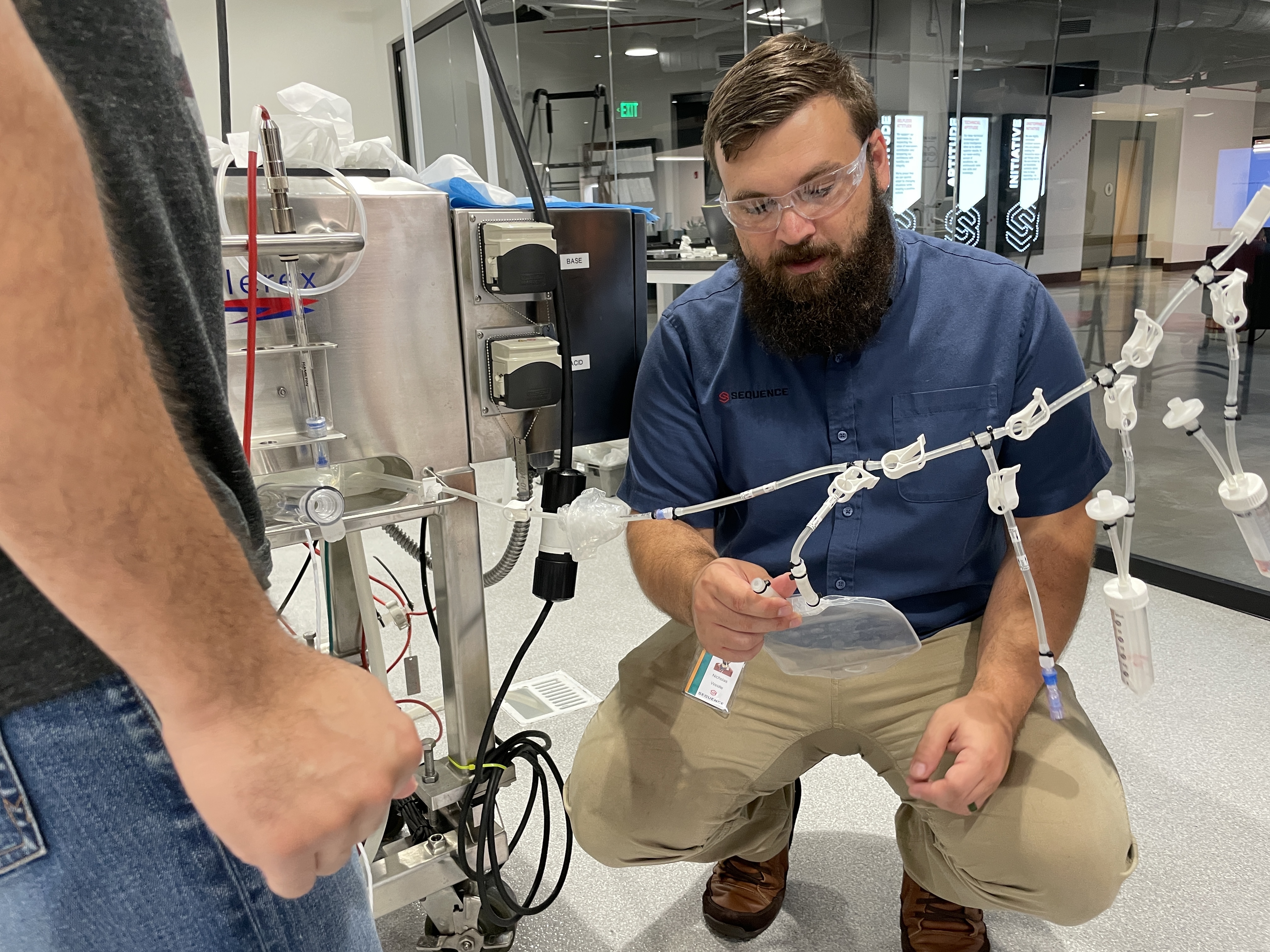